Rock Specimen Polishing in the Field
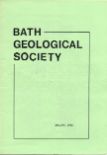
Few geologists realise how easy it is to polish a small flat or ‘window’ on a specimen by hand. It is often better to do this than to expose the centre by breaking. For example, one may find a pebble in Scotland coated with a surface like a walnut. It may be an agate, but if it is broken it will almost certainly be ruined by the fine cracks which will run in all directions. It is far better to polish a small flat thus revealing the interior. In other cases the contrast between the broken and polished surfaces is remarkable and a useful aid to identification.
How does one go about polishing in the field? Simplicity is essential so kit is limited to three sheets of wet or dry silicon carbide paper (80, 220 and 600 grits) each stuck down to a sheet of waterproof plywood with waterproof adhesive. A piece of broken grinding wheel or a builder’s silicon carbide rubbing block is useful at first if the surface is very rough.
The procedure is to dip the rubbing block in water and then to hold it rigidly in the left hand. The specimen is held in the right hand and by pivoting the elbow and keeping the wrists rigid a flat is soon ground. Plenty of water is used and a little soap helps. The next stage is to use the 80 grit wet or dry paper in the same fashion until the required structure is exposed. The process is repeated with the 220 grade and the specimen is then thoroughly washed to remove every grain of grit, after which the 600 grade is used, again wet, to produce a fine satin finish. Whilst wet this gives some idea of the polished finish and is usually adequate for field work. However, when dry the surface becomes dull and opaque and although it can be improved by a coat of clear nail varnish, it will be very inferior to a fully polished finish.
Final polishing is usually tackled back at home where the specimen can be thoroughly washed and clean conditions can be maintained. Cerium oxide powder is used and the polishing surface may be of wood, leather, perspex, hard felt or cloth according to the properties of the specimen. A good first try is a clean sheet of plywood. A few drops of water are put in the centre of the wood followed by a pinch of cerium oxide. The specimen is then worked over the wood, firstly with light pressure to spread the powder evenly and then with increasing pressure to produce the polish. The art is to keep the wood nearly dry so that there is a strong drag between the paste and the specimen. This indicates polishing and with experience one can tell when the polish has developed and when to stop. If all is well the polish will develop quite rapidly and it is necessary to practice a little as it is easy to go on too long in the hope of improving. Usually this results in a gradual deterioration in flatness and the development of what is called ‘orange peel’, a polished but pitted surface.
A most important point is to keep the wood very clean, whenever it is not in use wrap it in clean paper. A single grain of grit in the surface will render it useless as it will scratch the stone all the time it is being polished.
This may all seem complicated but you may rest assured that it is not. The skills are much easier to demonstrate (and to learn) than to describe. I suggest that anyone to be shown, or better still visits their local Lapidary Society when they have a hand polishing session. This is ideal for beginners as they are able to practice with someone on hand to advise. All materials are provided, even the rocks if you are short, so do come along and have a try.